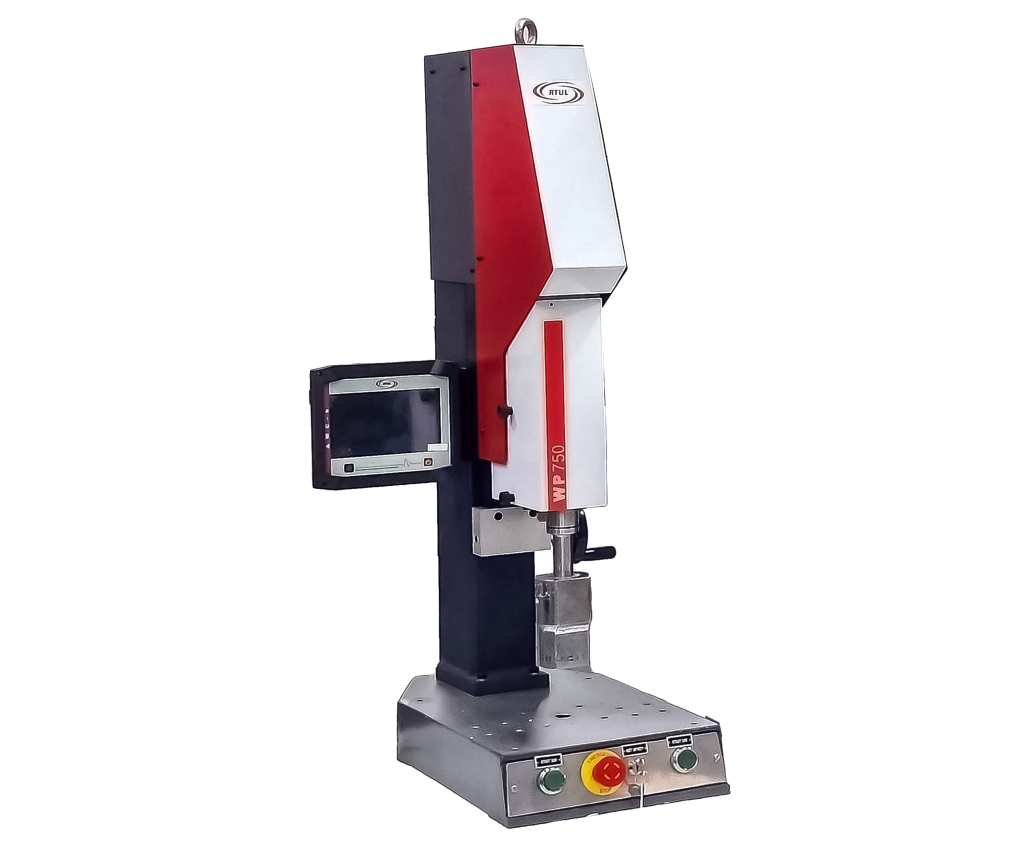
Today’s industrial production and operations require agile processes to save time and money. Ultrasonic welding (USW) is a crucial process used for joining materials like metal and plastics components. With advanced technology and solid mechanical vibrations, it is the fastest method by which results are achieved.
RTUL is a market leader which deals in making components for industries like automotive, aerospace, appliances, electronics and medical devices. As a reliable ultrasonic machine manufacturer in India our experts understand the nature of welding systems where melting is not required.
Bonding different materials & challenges
The scale of grain and delicate mechanical properties require disparate techniques for creating successful joints. That is why custom Ultrasonic welders know how to bring optimal results. When it comes to metallurgic joints various alloys like Aluminium, Nickel, Titanium, Magnesium and steel are blended. Thermoplastics and reinforced composites combinations also make the grade. This method does not damage the material properties during high frequency vibrations. It is a reliable and established process which provides solid state bonding.
Setting standards for joining materials
We have experts who apply innovation and in-house expertise as required by industrial applications. Ultrasonic metal welding is best applied for wiring harnessing assemblies, power electronics joints and battery cell productions. The standard and quality relies on validating the joints with destructive testing. Disturbances are measured with relevant number of welds. Guidelines are given to detect material surface changes, thickness, hardness, rolling direction and position of welding. Experts weigh the horns and anvil vibrations, penetration levels on high-frequency.
We apply different process which rules your industry standard. Thus our challenge lies in identifying the right technique.
For joining we use welding with:
- Ultrasonic
- Laser
- Thermal
- Clean vibration
- Spin
- Infrared
- Hot plating
An in-depth analysis is done to choose the right method for testing the prototype. Once the testing is successful and the right solution is found it enables production scalability with precision.
Markets and Applications
Custom Ultrasonic Welders are always in demand and important for various products. They are normally used for automotive, appliances, medical sector, battery, refrigeration, electric & electronics, aerospace, air conditioning, and solar energy panelling. The future opportunities are increasing as all these sectors require better ways to fulfil their customer requirements with various types of Ultrasonic welding components and designs.
End Benefits & Acceptance
There are many reasons why Ultrasonic metal welding is being accepted in several sectors.
The visibility can be seen in the preparation of a good product which has the following:
- Technology is eco-friendly and does not hurt the environment
- The process and techniques used are efficient
- Only 1/30th of the energy is discharged during resistance welding
- No need for any another material to be added after joining
- Eliminates the need for contaminated products to combine like flux agents, solvents, solder or crimp connectors
With ultrasonic instrumentation and high-profile products like transducers, we develop the latest processes for manufacture of metal, plastic welding and cleaning equipment. Our experts look forward to meeting challenges with your industry’s specific metal welding requirements.