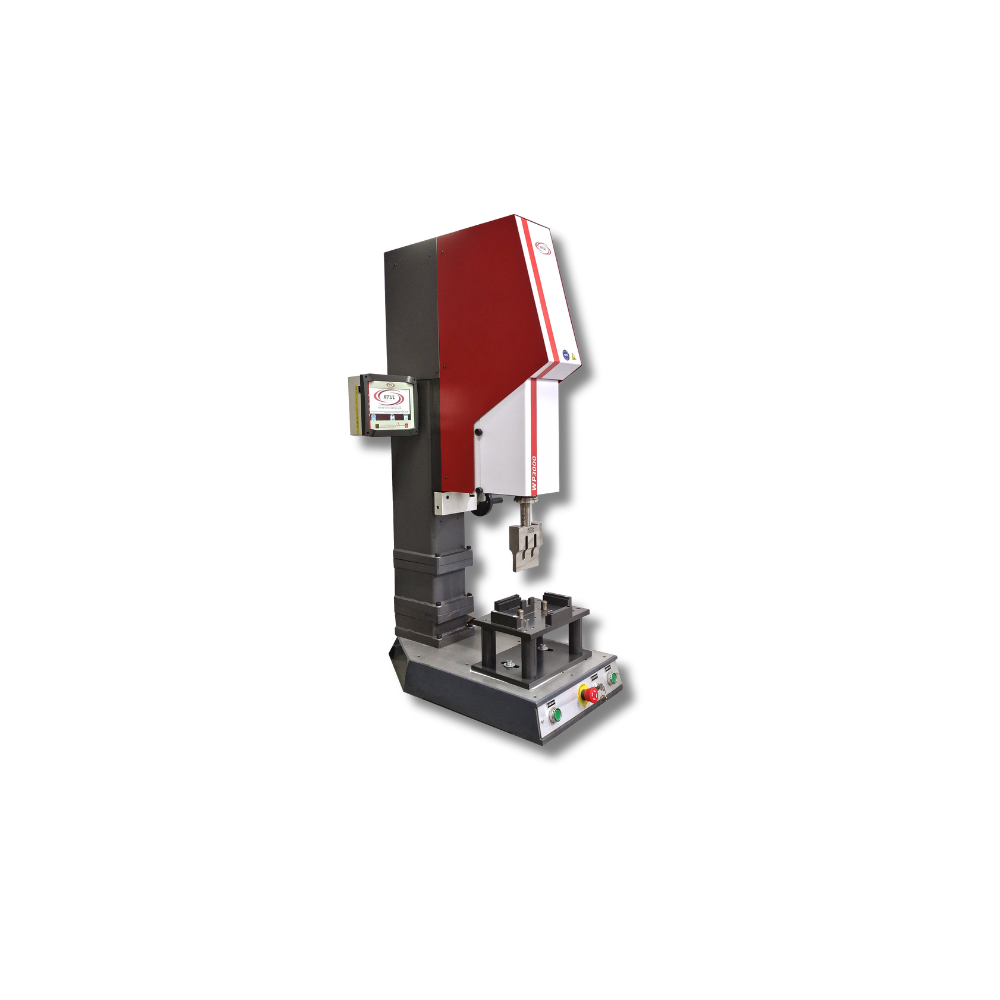
An ultrasonic welding machine is operational in diverse industries ranging from medical, packaging, automotive, and aerospace. Its wide applications are feasible in electronic & IT, making it valuable and versatile.
To understand its overall utility, we focus on the machines and tools involved to get optimal results. Different techniques are involved to increase its outcome.
This guest post features:
- Why choose an Ultrasonic welding machine?
- Anatomy of the equipment & working mechanisms
- Tooling and Investment feasibility
Engineers making use of this equipment require appropriate machine design and tools to conduct the processes. Hence, there are various options available to collaborate with manufacturers to hire or invest. Based on specific applications it is vital to choose the right ultrasonic cleaning machine. Welding is determined by:
- Size of the part
- Compatibility of materials
- Performance
- Costs involved
- Requirements of parts
Most buyers find ultrasonic plastic welding indispensable for their processes. As they understand the configuration and elements, the benefits are multiple.
Welding works on the principle that any two compatible materials will be subjected to high friction and vibrations by the machine. The activation generates heat and sends energy to specific areas of the joints. The two components are plasticized when pressure is applied in the welding zone. Most engineers prefer this method as it is agile, homogenous, and forms a very robust bond.
Ultrasonic plastic welding works on this principle.
Process involvement
There are no two machines that are alike in their functionality. Many models have been introduced in the market over the years. But the key drivers for each one rests on reliability, simple applications, and stability.
As the new generation of machines improves, they are used for:
- Spot Welding
- De-gating
- Reverting
- Inserting
- Swagging
- Component welding
The choice of equipment will always depend on the function and industrial usage. But a basic ultrasonic welding machine will have a few common elements.
They are:
- Flexibility for welding components and their working frequency. The method will have 20 to 40 KHZ and ultrasonics being changed when required.
- It has a large power range with 400 to 5000 W input.
- Monitoring for welding conditions that target power, collapse, energy, and time position.
- The machine comes with a warranty and standard options like part sensing and ejection, barcode reader and linear encoder.
A good piece of equipment is easily recognized by the engineers. A quality ultrasonic welding machine will remain rigid when it is activated. When pressure is applied it will not vibrate or break down. The most important facet is the control and programming that can be done for welding. Manufacturing is tracible and meets ISO standards.
Ultrasonic tooling is an integral part and involves components like sonotrodes. Accessories like fixers have specific jobs. Depending on the industrial application, they are designed. Tooling can be done for different frequencies. Various materials like metals are used to make them.
If you are looking for a specific design for your needs, do let us know. For large projects investing in the machine is a wise decision. Our products meet efficiency and productivity needs in several industries. Consult our engineers to get the best deal.